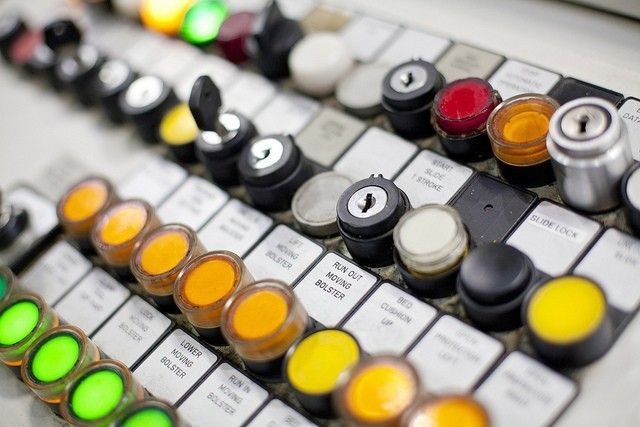
Tesla Motors just released the first segment of its "Inside Tesla" video series. At the forefront of all-electric vehicle propulsion, the "Inside Tesla" series shares a glimpse of just what it takes to produce Tesla's latest Model S sedan as the company begins to count down the days to Model S customer delivery.
In this particular episode, Tesla takes us through its stamping process of the steel-reinforced aluminum car. According to Tesla, aluminum has been used extensively in the Model S to reduce weight in order to make gains in efficiency and range.
First, rolls of enormous aluminum coil, each weighing 20,000 pounds, are fed into the Blanking Line machine that cuts the coil into rectangles of manageable size, known as "blanks."
Next, Kuka robots are responsible for moving the aluminum blanks for the Press line, where molds, each weighing 40 tons, compress at a force of over one thousand tons to stamp, form, trim and pierce these aluminum pieces. Also known as "dies," each mold is design-specific to a particular component of the Model S, allowing Tesla to produce its large panels, from doors to engine covers, in-house rather than to outsource production. Tesla also claims that its press line is the largest of its kind in North America.
Have a look at the short video below to see how stamping process in action. Capturing the efficiency of its automation, what the video fails to capture is just how immense the size and scale of the factory is.
Tesla expects to deliver over 5,000 Model S sedans this year. Delivery begins on June 22, 2012.
3